В глиноземном производстве наиболее сложными с точки зрения обрушения являются приемные бункера бокситов участка мокрого размола. Сложность обеспечения обрушения сводов связана как с конструктивными особенностями бункеров: большая емкость (порядка 1000 тонн), большая толщина боковых стенок, мощное оребрение; так и со свойствами загружаемого материала – бокситов, характеризующихся высокой влажностью (загрузка происходит обычно с открытых складов), высоким содержанием мелкодисперсной фракции, склонностью к слеживанию и слипанию.
С 2010 года на Николаевском глинозёмном заводе (ООО «НГЗ») решена проблема, связанная с подачей бокситов из приёмных бункеров в шаровые мельницы, посредством внедрения магнитно-импульсных установок ИМ производства ООО НПП «МИТЭК».
Применяемые ранее способы и устройства не обеспечивали равномерную подачу бокситов, что приводило к технологическим нарушениям, увеличению холостой работы шаровых мельниц, а также сказывалось на количестве и качестве выпускаемой продукции.
Хранение бокситов на открытых складах приводит к его повышенной влажности, до 20%. В осенне-зимний период это способствовало его примерзанию к стенкам бункеров.
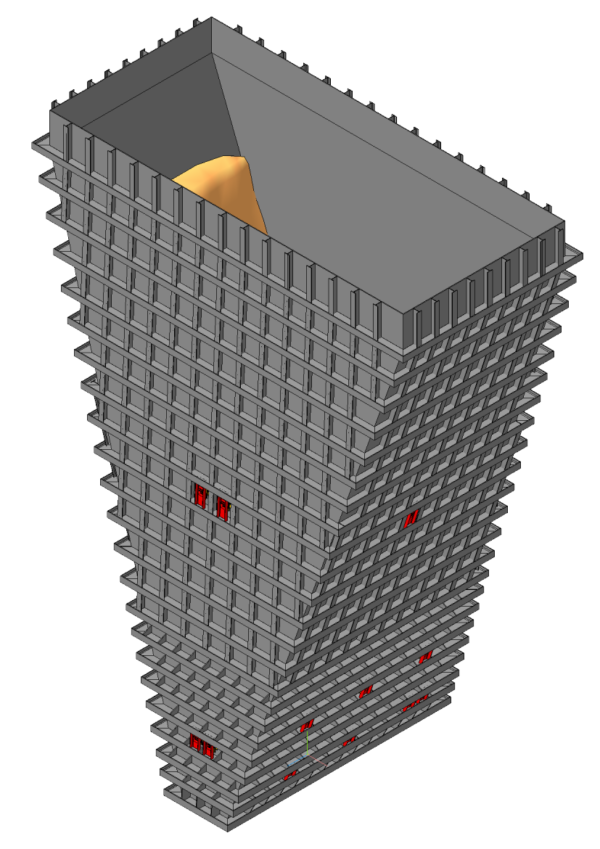
ООО НПП «МИТЭК» совместно со специалистами ООО «НГЗ» и проектно-конструкторским отделом ООО «СЦ «Металлург» разработали наиболее эффективные технические решения, апробирование которых состоялось в 2009 году. В это время проводилось строительство нового, 7-го бункера участка мокрого размола, предназначенного для приёма Гайянского боксита, характеризующегося высокой склонностью к зависанию.
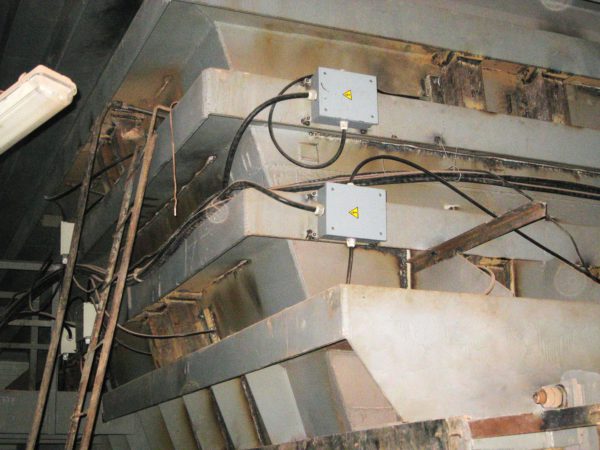
Оснащение приемного бункера боксита макетом установки ИМ5-2,4-8
Предприятие «МИТЭК» с использованием макета магнитно-импульсной установки ИМ5-2,4-8 провело испытания по проверке эффективности обрушения сводов зависших масс с использованием нового варианта конструкций узлов креплений исполнительных механизмов, их количества и мест размещения. Реализовано воздействие на вибрационные листы, закреплённые специальным образом на внутренних поверхностях бункера.
В ходе испытаний отработан алгоритм работы установки с автоматическим включением от датчика наличия материала на пластинчатом питателе. Оптимизировано необходимое для эффективного обрушения количество исполнительных механизмов, места их размещения и последовательность включения в процессе выгрузки материала из бункера. В результате достигнут эффект обеспечения полного выхода материала из бункера без применения размывания боксита водой и без привлечения оператора в процессе его выгрузки.
В 2010 году после проведения успешных испытательных работ по определению эффективных конструкторских и схемных решений на участке мокрого размола Николаевского глиноземного завода внедрены две установки:
ИМ5-1,8-24 – на 3 приемных бункерах бокситов (первый и второй ярусы);
ИМ5-1,8-16 – на 2 приемных бункерах бокситов (первый и второй ярусы).
В 2014 году оставшиеся 2 приёмных бункера были оснащены установкой ИМ5-1,8-16, а также все семь бункеров были дополнительно оснащены ещё одним, третьим, ярусом исполнительных механизмов магнитно-импульсной установки ИМ5-1,8-14.
Схема оснащения бункеров ООО «НГЗ» установками ИМ:
Применение магнитно-импульсных установок ИМ позволило обеспечить быструю и эффективную очистку бункеров без использования воды, ручного труда, исключить внеплановые простои и оптимизировать производственный процесс.
Установки работают надежно и эффективно! В качестве подтверждения приводим отзыв директора по производству ООО «НГЗ».
Карта внедрений
Магнитно-импульсные установки ИМ:
- обеспечивают уверенный выход материала из оснащенных бункеров;
- производят очистку стенок бункеров от налипшего материала;
- обеспечивают эффективную регенерацию фильтров;
- работают в энергосберегающем режиме, эксплуатационные затраты минимальны;
- в основном не требуют реконструкции бункеров при их оснащении;
- не нарушают целостности стенок бункеров;
- совместимы с тензометрическими системами контроля веса материала в бункерах;
- соответствуют требованиям Директив и гармонизированных норм технического регулирования Евросоюза по электробезопасности и электромагнитной совместимости;
- применимы во взрывоопасных зонах класса 22, опасных по воспламенению горючей пыли в соответствии с Директивой АТЕХ;
- легко интегрируются в современные автоматизированные системы управления технологическими процессами;
- надежны и долговечны (по техническим условиям – 10 лет, на практике некоторые установки уже эксплуатируются более 25 лет).