In the production of cereals and compound feeds for hoppers and consumable silos, overhead, operational, macrodosing, a storage of raw materials, the following types of magnetic-impulse installations IM3-0.8-n, IM3-1.1-n, IM3-1.5-n (where n is the number of installation channels – two executive mechanisms in each channel). The installations have been introduced and are successfully operating at such enterprises as “Myronivsky plant for the production of cereals and animal feed”, “Tavriysky combined feed mill”, “Dneprovsky poultry plant”, “Boryspil feed mill”, “Katerinopolsky elevator” and many others (see the list of implemented installations).
An example of equipping hoppers with a magnetic-impulse bridging system based on the IM installation is shown in the following diagram:
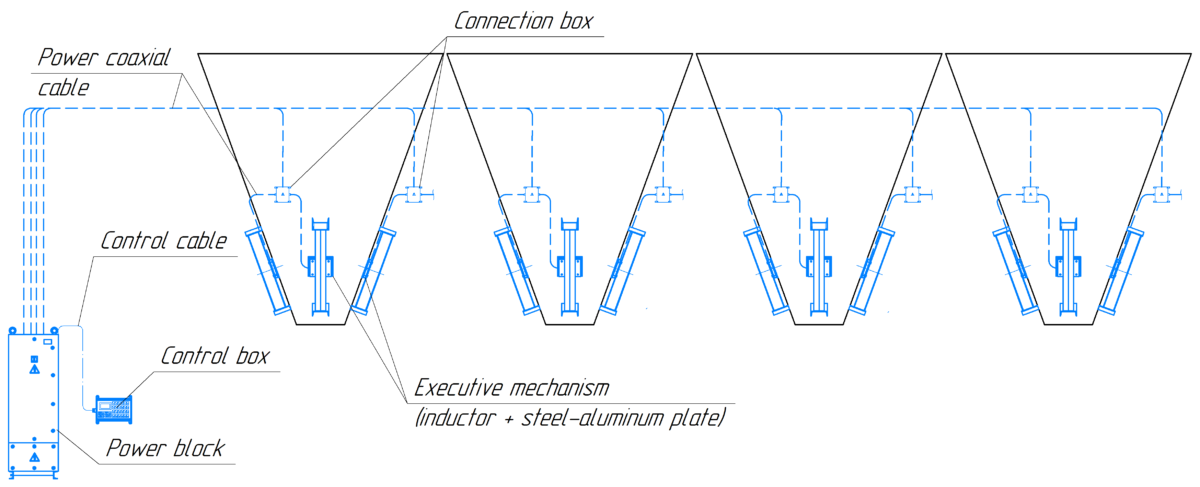
As a result of the implementation, the customer receives a guaranteed effective solution for the timely release of materials from the hoppers, which ensures the continuity of the production process. It is also worth taking into account the proven in practice long-term trouble-free operation of magnetic-impulse installations IM with minimal attention from the maintenance personnel, as well as maintaining the integrity of the structure of hoppers, silos, chutes and other objects equipped with IM installations.
Implementations map
Magnetic-impulse installations IM:
- ensure a sustainable release of material from equipped hoppers;
- clean the walls of hoppers from adhered material;
- provide efficient filter regeneration;
- operation in an energy-saving mode, operating costs are minimal;
- basically do not require reconstruction of hoppers when equipping them;
- do not violate the integrity of the walls of the hoppers;
- compatible with strain gauge systems for controlling the weight of material in hoppers;
- comply with the requirements of the Directives and harmonized technical regulation of the European Union on electrical safety and electromagnetic compatibility;
- applicable in hazardous areas of class 22, hazardous by ignition of combustible dust in accordance with the ATEX Directive;
- easily integrated into modern automated process control systems;
- reliable and durable (according to technical conditions – 10 years, in practice, some installations have already been in operation for more than 25 years).