There are many objects in coke production where there lots of problems with arching and hanging of bulk materials, sticking and freezing to the walls of containers.
Due to the design features of these objects, the installations IM with power capacity above the average are mainly used, such as IM3-1,9-n, IM3-2,3-n, IM4-1,8-n, where n is the number of channels from 1 to 16, 2 executive mechanisms per channel.
We recommend considering the several examples of equipping CP facilities with magnetic-impulse installations IM.
Closed coal warehouses
The design of a closed coal warehouse usually consists of a line of twin reinforced concrete silos with a metal cone part, in each group of which the bulk material of various characteristics is stored. Dosing conveyors or feeders supply the material to the collecting conveyor. In this case, the exact dosing of each component and their layered mixing must be observed, that enables obtaining the mixtures of a given composition.
Violation of the timely supply of any of the components onto the assembly line leads to a forced stop of the line. The possible reasons for arching and hanging of materials are the design features of silos and funnels, low temperatures for high-moisture material, significant compaction of the material when falling during loading of silos, adhesion properties and instability of other physical and mechanical characteristics.
To solve these problems, manual labor is often engaged using the sledgehammers or more powerful percussion tools, that leads to such consequences as
- deformation of the walls, where even more complex hangings of materials are formed,
- destruction of welded joints and bases of fastenings of the entire structure of the hopper,
- frequent injuries to service personnel.
In addition to the low efficiency of this method of arches collapsing, one has to put up with the frequent shutdowns of prosessing lines for unscheduled repairs.
Until recent times, the electric vibrators and pneumatic impulse systems were considered as the traditional mechanical systems for elimination of hanging.
- The electric vibrators are short-lived, often lead to the destruction of the walls of hoppers, to the compaction of the material in the hopper.
- The pneumatic systems require the generation and preparation (drying) of high pressure air, and are inefficient in case of material freezing.
Since the beginning of the 90s, in order to eliminate the hang-ups of bulk materials, electric vibrators and pneumatic systems have been replaced by efficient and economical in operation the magnetic-impulse installations IM manufactured by RPE “MITEK” LLC. They have a number of advantages compared to their predecessors, namely:
- possibility of prompt adjustment of the amplitude, shape and repetition rate of the acting impulses;
- possibility of not only collapsing the suspended material, but also cleaning the surface (hopper wall) from adhering material;
- work in energy-saving mode with minimal operating costs;
- preservation of the integrity of the cleaned walls of hoppers and other surfaces;
- ease of operation, maintainability, durability. The service life of IM installations before overhaul is at least 10 years.
As an example, below is a diagram of equipping 28 silos of a closed coal warehouse of the coal preparation workshop of CP
Receiving hoppers under railcar dumpers
In general, the planned unloading capacity of railcar dumpers is up to 30 railcars per hour. It should not take more than 2-3 minutes to unload each railcar. The ensuring of sufficient throughput and unloading speed of receiving hoppers is a fundamental task, on which the main performance indicators depend.
Hoppers must withstand the load of material falling from the height of 15-20 m, which is supplied in large volumes (up to 150 tons). Therefore, they are made of thick-walled and rigid-ribbed structures, lined with armor plates. The material, fed into them is of different dispersion, wet, and often frozen.
The most efficient and reliable way to eliminate the hanging of materials in the hoppers under the railcar dumpers is the use of magnetic-impulse cleaning systems. None of the known alternative methods can compete with the installations IM manufactured by RPE “MITEK” LLC.
This is evidenced by the lots of successful implementations of magnetic-impulse installations IM on hoppers under railcar dumpers, including coke production.
Here is the scheme of equipping the hoppers under the railcar dumpers № 1 and № 2 Coke production
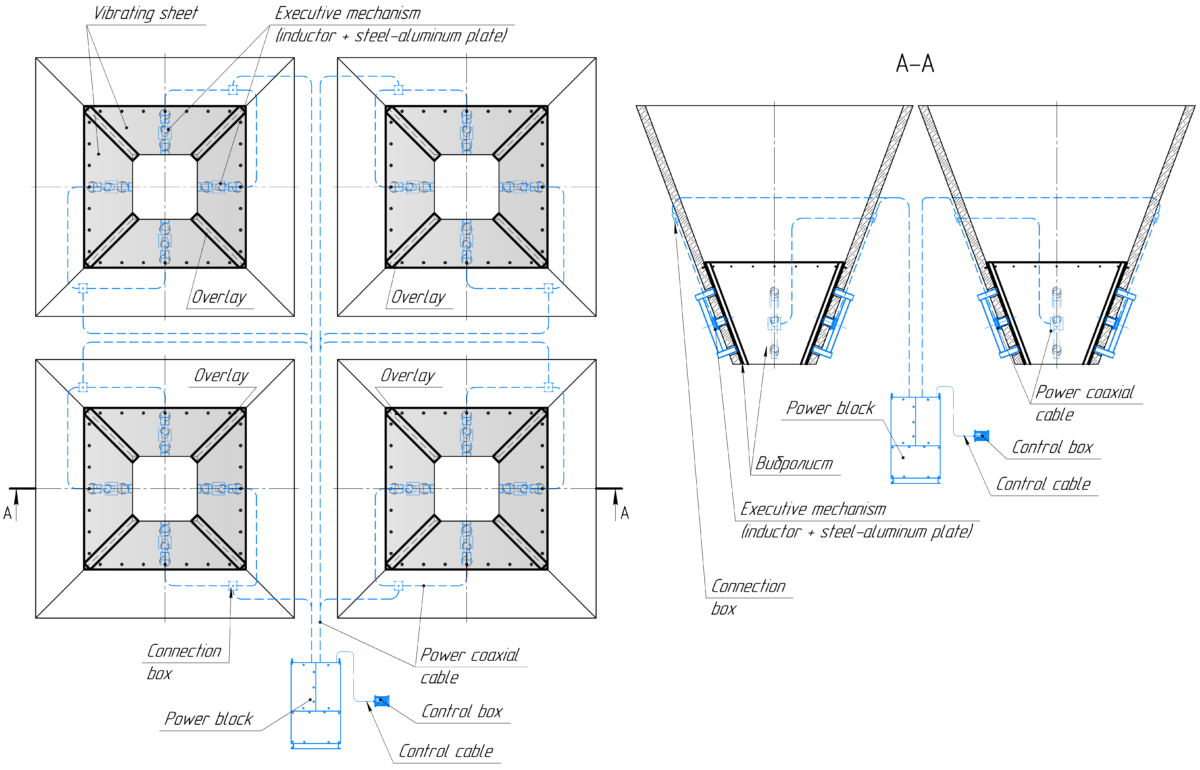
Implementations map
Magnetic-impulse installations IM:
- ensure a sustainable release of material from equipped hoppers;
- clean the walls of hoppers from adhered material;
- provide efficient filter regeneration;
- operation in an energy-saving mode, operating costs are minimal;
- basically do not require reconstruction of hoppers when equipping them;
- do not violate the integrity of the walls of the hoppers;
- compatible with strain gauge systems for controlling the weight of material in hoppers;
- comply with the requirements of the Directives and harmonized technical regulation of the European Union on electrical safety and electromagnetic compatibility;
- applicable in hazardous areas of class 22, hazardous by ignition of combustible dust in accordance with the ATEX Directive;
- easily integrated into modern automated process control systems;
- reliable and durable (according to technical conditions – 10 years, in practice, some installations have already been in operation for more than 25 years).