Magnetic-impulse installations IM are widely used in the chemical industry. Many bulk materials used as raw materials or finished products in various subsectors of the chemical industry (organic and inorganic chemistry, pharmaceuticals, agrochemistry, ceramics, etc.) need additional stimulation when unloading from hoppers and transporting along the technological lines. For example, such objects are equipped with IM installations as:
- cargo handling units for a mixture of mineral fertilizers and granulated blast-furnace slag;
- hoppers with bulk additives;
- chutes of the unit for drying-calcining of aluminium fluoride;
- receiving hoppers of potassium chloride;
- silos with soda;
- storage hoppers of sylvinite ore;
- installation of a fluidized bed;
- supply hoppers with chalk;
- zinc oxide silos;
- etc., a complete list of implementations of installations IM in the chemical industry.
Examples of equipping some production facilities with installations IM
In the manufacture of tires in Finland, a variety of pneumatic systems on zinc oxide silos have been previously used that have proven to be inadequate for efficiency and performance. Here are the photographs of the working bodies of these pneumatic systems:
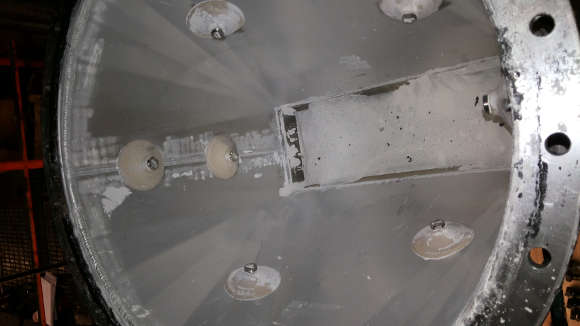
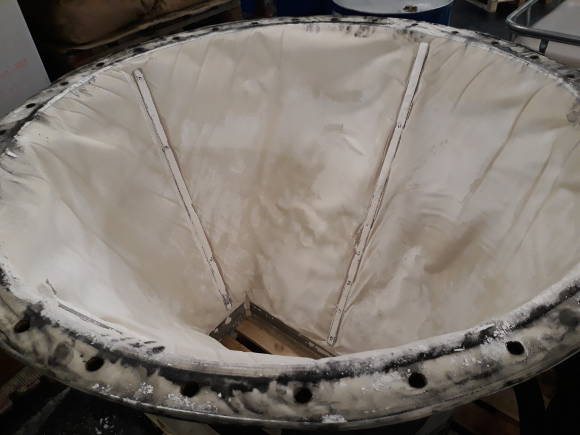
In 2017, low-efficient pneumatic systems were dismantled and replaced with a magnetic-impulse installation IM manufactured by RPE “MITEK” LLC:
Display of the operation of the installation IM at this enterprise:
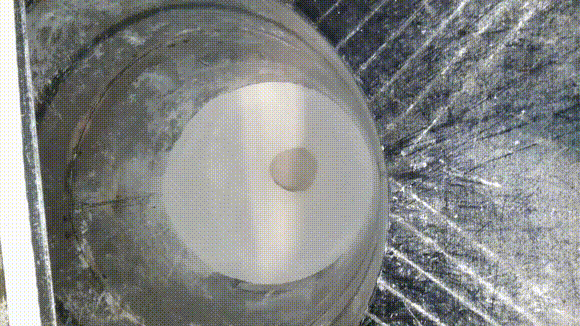
After evaluating the advantages of installations IM, the Customer decided to further equip zinc oxide silos with only our equipment. So, in 2018, another installation IM was purchased, and in 2021 a new silo was equipped with one of the channels of the previously purchased installation IM.
Operation of installations IM in aggressive environments
To ensure a long service life of magnetic-impulse equipment in chemical production conditions under the influence of aggressive environment (high humidity, acid fumes, alkaline suspensions, extreme temperature conditions), a number of technical solutions have been developed that are used in the manufacture and implementation of installations IM. Here are some of them:
- design of the control panel and plastic connection boxes with IP66 degree of protection;
- application of an additional coating of inductors with a dielectric material resistant to the effects of an aggressive environment;
- use of original design solutions that ensure the integrity of steel-aluminum plates during operation in an aggressive environment;
- increasing of the length of the cable inserted into the inductors by the amount necessary to remove the connection boxes from the zones of increased evaporation;
- implementation of a multi-layer paint-and-varnish coating of metal elements of installations IM exposed to an aggressive environment.
The following photos show examples of equipping the facilities of chemical enterprises with an aggressive environment by IM installations. Among them are hoppers of substandard material, chutes of the cargo handling unit of the complex mineral fertilizers section and the hopper of the loading section in the cities of Cherepovets and Kirovsk, equipped by executive mechanisms of magnetic-impulse installations IM.
Here is the review of operation of the first IM installation at one of these enterprises.
Hoppers of final products of the workshop for loading into railway cars in the city of Soligorsk, Republic of Belarus, equipped with an IM installation are shown in the photo below. We suggest to learn the feedback on the operation of the IM installations at this enterprise.
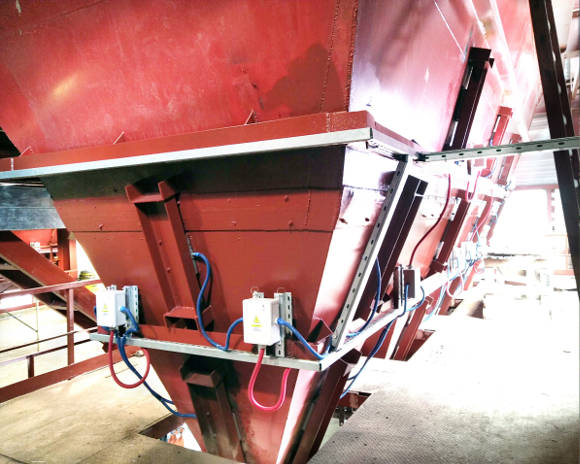
Summing up, we can summarize that the magnetic-impulse installations IM have found application at all stages of the production cycle.
Starting from the receiving bunkers of raw materials and ending with the loading of finished products into wagons, IM installations successfully cope with the task and are in increasing demand, replacing outdated methods of cleaning containers – electric vibrators, pneumatic systems and manual labor.
The dynamics of the increase in the number of repeated orders of the IM units testifies to the high assessment of the quality of our products, which satisfies the various requirements of the Customers.
Implementations map
Magnetic-impulse installations IM:
- ensure a sustainable release of material from equipped hoppers;
- clean the walls of hoppers from adhered material;
- provide efficient filter regeneration;
- operation in an energy-saving mode, operating costs are minimal;
- basically do not require reconstruction of hoppers when equipping them;
- do not violate the integrity of the walls of the hoppers;
- compatible with strain gauge systems for controlling the weight of material in hoppers;
- comply with the requirements of the Directives and harmonized technical regulation of the European Union on electrical safety and electromagnetic compatibility;
- applicable in hazardous areas of class 22, hazardous by ignition of combustible dust in accordance with the ATEX Directive;
- easily integrated into modern automated process control systems;
- reliable and durable (according to technical conditions – 10 years, in practice, some installations have already been in operation for more than 25 years).