In alumina production,the receiving hoppers of bauxite in the wet grinding section are the most difficult in terms of collapsing. The difficulty of ensuring the collapsing of the arches is associated both with the design features of the hoppers: large capacity (about 1000 tons), large thickness of the side walls, tight ribing; and with the properties of the loaded material – bauxite, characterized by high humidity (loading usually occurs from open warehouses), a high content of fine fraction, a tendency to caking and sticking together.
Starting from 2010, at “Mykolaiv Alumina Refinery” (“MAR” LLC) the problem, associated with the supply of bauxites from receiving hoppers to ball mills has been solved through the implementation of magnetic-impulse installations IM manufactured by RPE “MITEK” LLC.
The previously used methods and devices did not provide a uniform supply of bauxites. It led to technological violations, an increase in idle operation of ball mills, and affected the quantity and quality of output goods as well.
Storage of bauxites in open warehouses leads to its high humidity, up to 20%. In the autumn-winter period, this contributed to its freezing to the walls of hoppers.
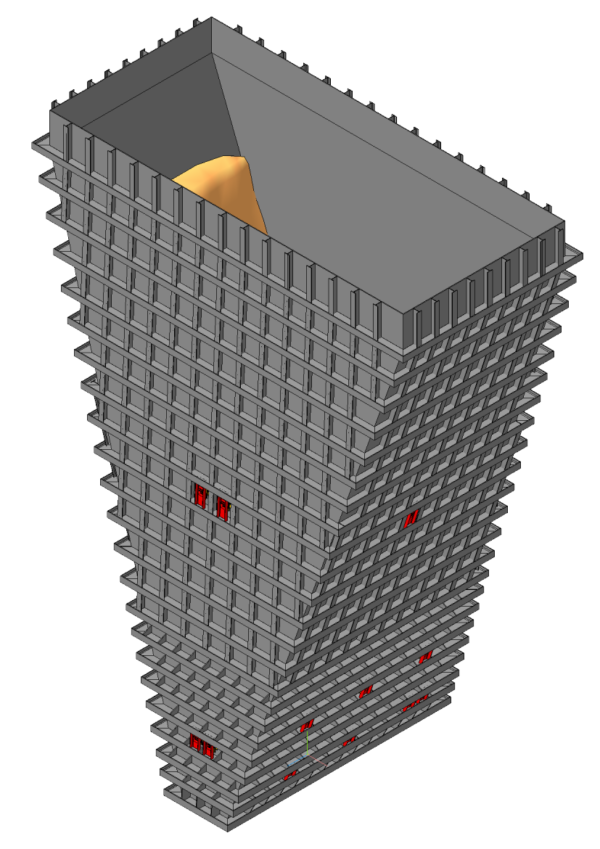
RPE “MITEK” LLC, together with the specialists from “MAR” LLC, and the design department of SC “Metallurg” LLC, developed the most efficient technical solutions, that were tested in 2009. At this time, the construction of a new 7th hopper of wet grinding section was underway, designed to receive the Guyanese bauxite. It is characterized by a high tendency to be hanging.
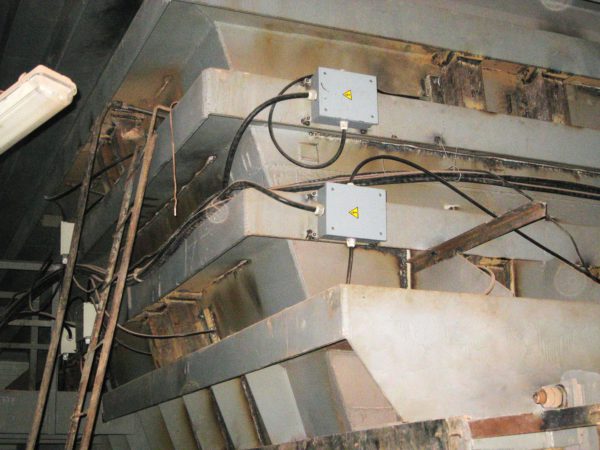
Equipping the receiving hopper of bauxite with a model of installation IM5-2,4-8
“MITEK”, using a model of IM5-2,4-8 magnetic-impulse installation, conducted tests to check the efficiency of collapsing the arches of suspended masses. The new version of design for attachment points of executive mechanisms, their number and locations was used. The effect on vibrating sheets, fixed in a special way on the inner surfaces of the hopper was produced.
During the tests, the algorithm of the installation operation with automatic switching ON from the material presence sensor on the apron feeder was worked out. The number of executive mechanisms required for efficient collapsing, their location and the sequence of switching on in the process of unloading material from the hopper have been optimized. As a result, the effect of ensuring the complete release of material from the hopper without the use of bauxite erosion by water, and without the involvement of an operator in the process of its unloading has been achieved.
In 2010, after successful test work to determine the efficient design and circuit solutions, two installations were implemented at the wet grinding section of Mykolaiv Alumina Refinery:
IM5-1,8-24 – on 3 receiving hoppers of bauxite (first and second tiers);
IM5-1,8-16 – on 2 receiving hoppers of bauxite (first and second tiers).
In 2014, the remaining 2 receiving hoppers were equipped with the IM5-1,8-16 installation, and all the seven hoppers were additionally equipped with one more third tier of the executive mechanisms of magnetic-impulse installation IM5-1,8-14.
Scheme of equipping the hoppers of “MAR” LLC with the installations IM:
The use of magnetic-impulse installations IM enabled to ensure the fast and efficient cleaning of hoppers without the use of water, manual labor, eliminate unscheduled downtime and optimize the production process.
The installations IM work reliably and efficiently! To confirm, we present the review of the Production director of “MAR” LLC.
Implementations map
Magnetic-impulse installations IM:
- ensure a sustainable release of material from equipped hoppers;
- clean the walls of hoppers from adhered material;
- provide efficient filter regeneration;
- operation in an energy-saving mode, operating costs are minimal;
- basically do not require reconstruction of hoppers when equipping them;
- do not violate the integrity of the walls of the hoppers;
- compatible with strain gauge systems for controlling the weight of material in hoppers;
- comply with the requirements of the Directives and harmonized technical regulation of the European Union on electrical safety and electromagnetic compatibility;
- applicable in hazardous areas of class 22, hazardous by ignition of combustible dust in accordance with the ATEX Directive;
- easily integrated into modern automated process control systems;
- reliable and durable (according to technical conditions – 10 years, in practice, some installations have already been in operation for more than 25 years).