Spray drying devices designed for drying whole milk, cheese whey, soya milk, melange, tea, dyes, blood, amino acids have problems associated with the adhesion of materials to the walls of drying chambers and cyclones.
The traditional method for solving these problems is the use of electro-mechanical and pneumatic hammers mounted on the outer surfaces of the walls of drying chambers and cyclones. The disadvantages of these devices include their low efficiency, low maintainability, and difficulty in maintenance.
Since the beginning of the 2000s, effective magnetic-impulse installations IM manufactured by RPE “MITEK” LLC have been used to eliminate the buildup of materials in spray drying systems.
At present, more than 100 installations IM have been introduced, designed to clean the walls of drying chambers and cyclones in spray drying devices A1-ORCH, A1-OR2CH, A1-OR2CH-1000, A1-OR3, Anhidro, VRA-4, etc., used mainly for milk powder production.
Drying tower equipped with a magnetic-impulse system IM:
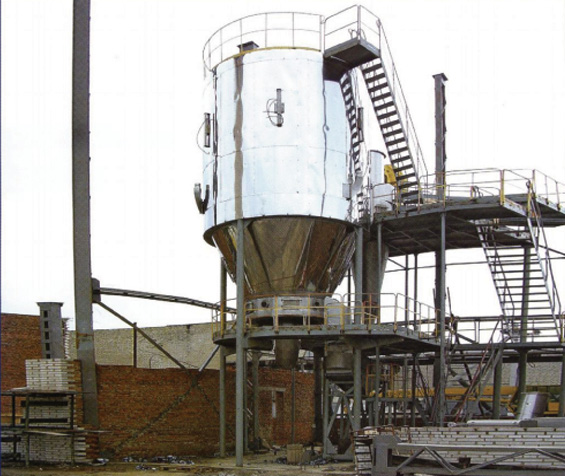
Cyclones equipped with a magnetic-impulse system IM:
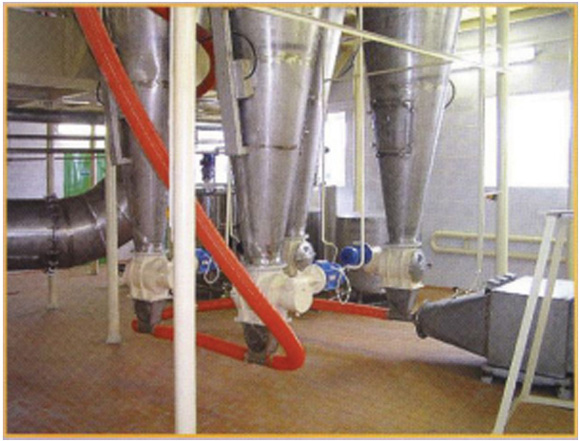
IM installations are serially completed with drying complexes manufactured by CJSC Kalinovskiy Machine-Building Plant, the deliveries of which are carried out both to Ukraine and abroad. IM installations have been introduced and are successfully operated at such enterprises as OJSC Akhtyrskiy Syrokombinat, SE Gadyachsyr, Laktis Branch of SE Aromat, OJSC Konotop Milk Plant, Litinsky Milk Plant, Mirgorod Cheese Factory LLC, Butter Cheese Plant “(Republic of Tatarstan), OJSC” Romensky Dairy Plant “, SE ” Ruzhin Moloko “, etc. (list of implementations).
Examples of equipping schemes for drying chambers and cyclones with IM installations
System for cleaning the walls of the drying chamber and cyclones based on the IM installation:
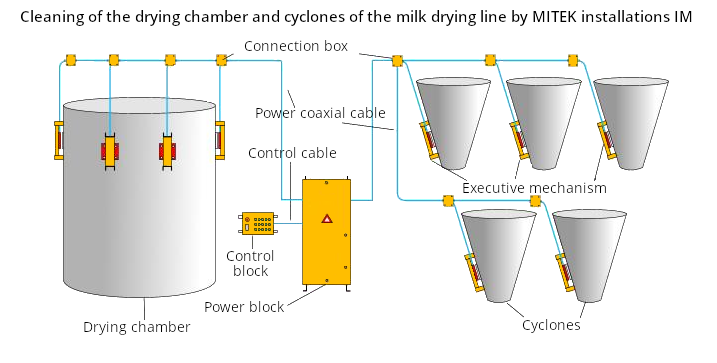
Mounting scheme of executive mechanisms of the drying chamber and cyclone wall cleaning system based on the IM installation:
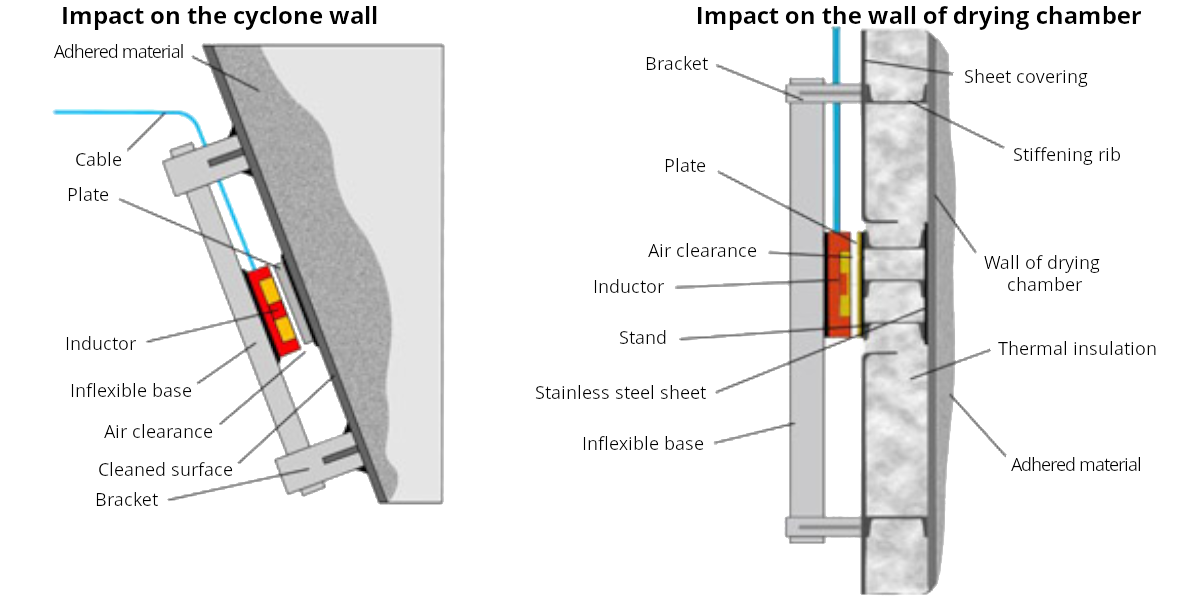
In most cases, the walls of the drying chambers are covered with heat-insulating material from outside. Therefore, the steel-aluminum plate owing to a simple metal structure is removed outside the thermal insulation coating.
In general, for magnetic-impulse systems of cleaning the walls of the drying chamber and cyclones, the IM1-1,2-n, IM1-2,4-n installations are used (n is the number of channels, 1 or 2 executive mechanisms per channel).
As a rule, when servicing drying systems, IM installations operate in automatic mode, successively sending a series of impulses to the activated channels. The strength of the mechanical action and the number of impulses are adjustable and are chosen sufficient to ensure the collapse of the adhered material.
For each type of drying spray system, the type of installation IM and the required number of executive mechanisms located on the drying chamber and cyclones are determined.
For example, in A1-ORCH drying system, IM1-1,2-11 installation is used with six executive mechanisms located on the drying chamber and five on cyclones, one mechanism on each cyclone:
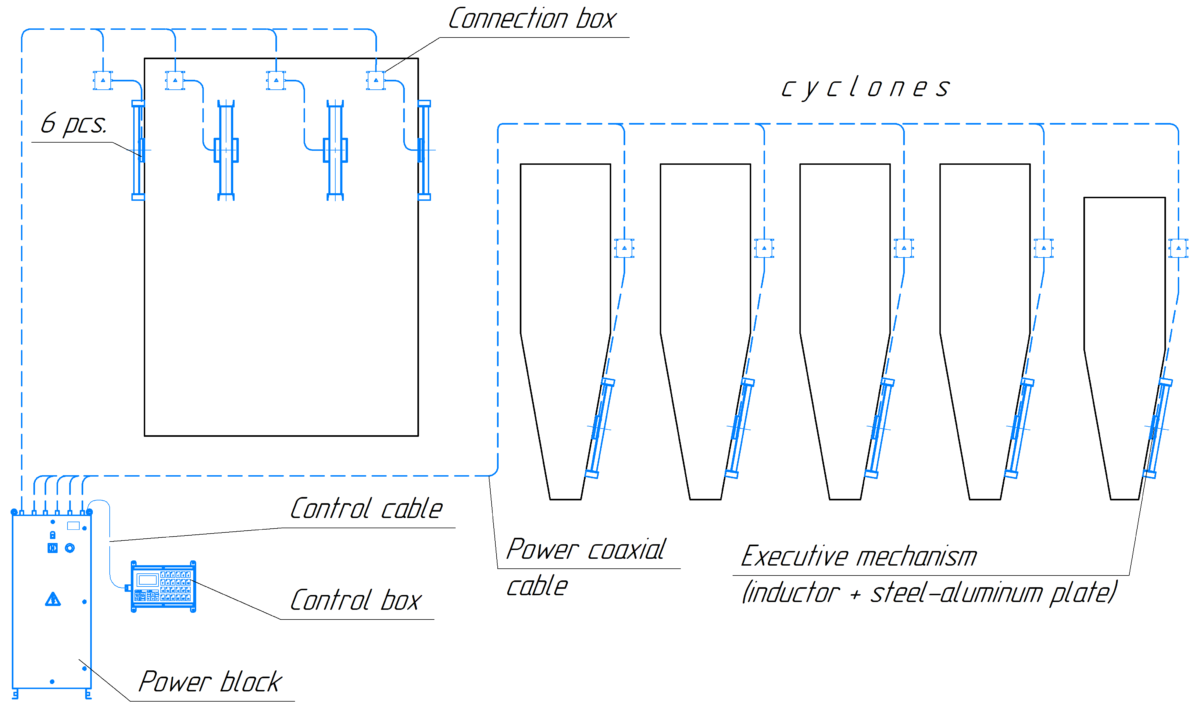
In the VRA-4 drying system, which has 3 cyclones, it is recommended to mount IM2-1,2-9 (two executive mechanisms in the channel) with the placement of six executive mechanisms on the cylindrical part of the drying chamber and six executive mechanisms on the conical part. Each cyclone is equipped with 2 mechanisms:
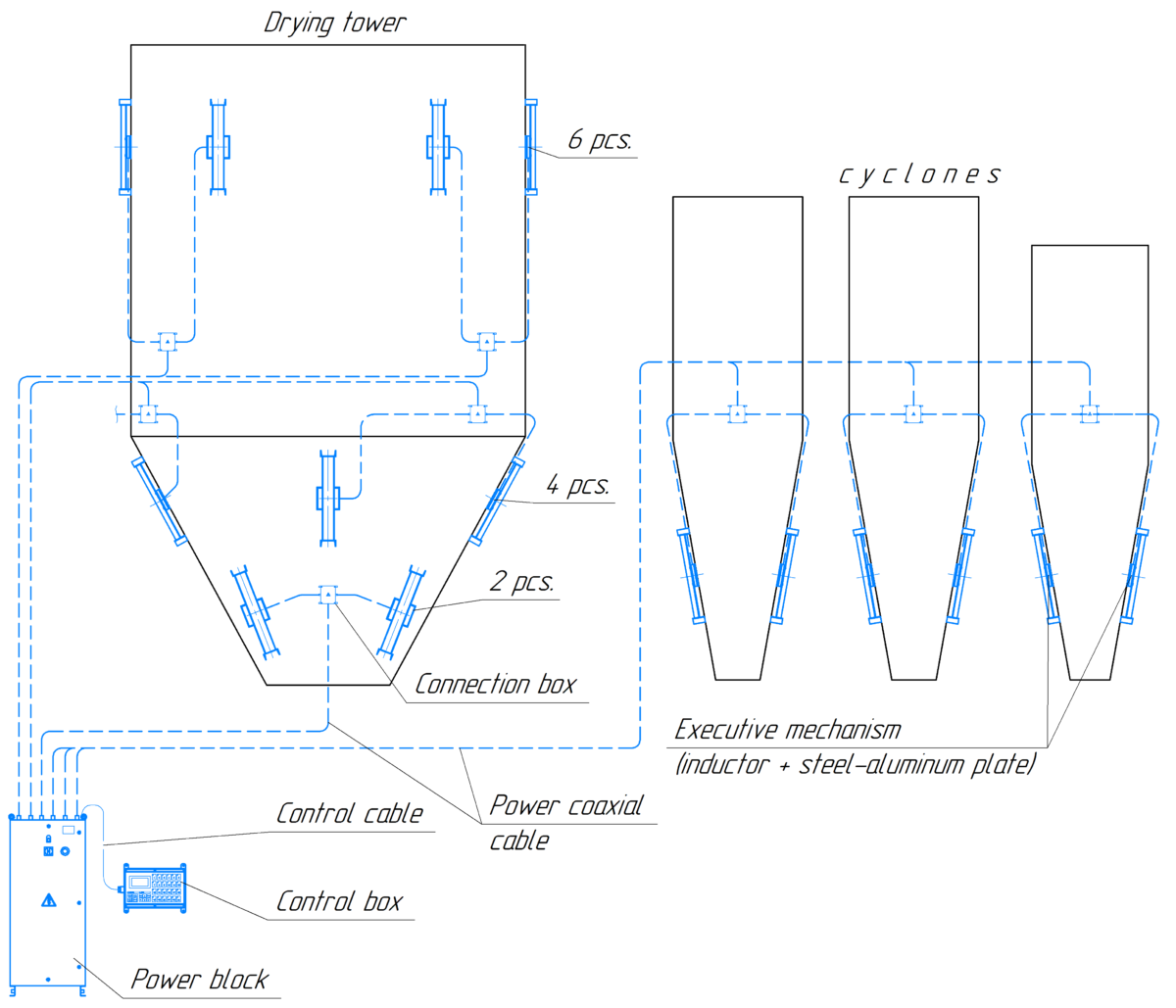
In A1-OR2CH drying system, IM2-1,2-8 installation is used with six executive mechanisms located on the cylindrical part of the drying chamber and four on the conical part. Each cyclone is equipped with one executive mechanism:
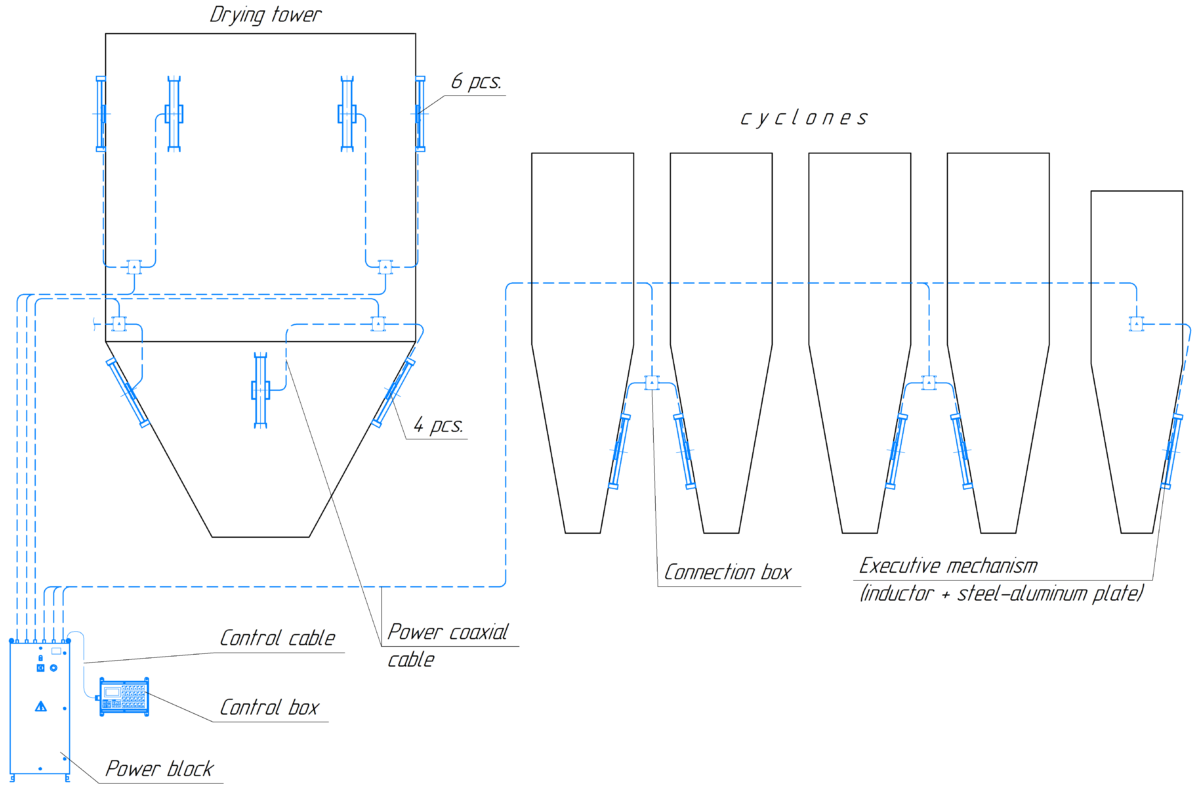
In A1-OR2CH-1000 drying device, the IM2-1,2-12 installation is used with eight executive mechanisms located on the cylindrical part of the drying chamber and five on the conical part. On four cyclones, 2 executive mechanisms are installed, on the fifth cyclone – one executive mechanism:
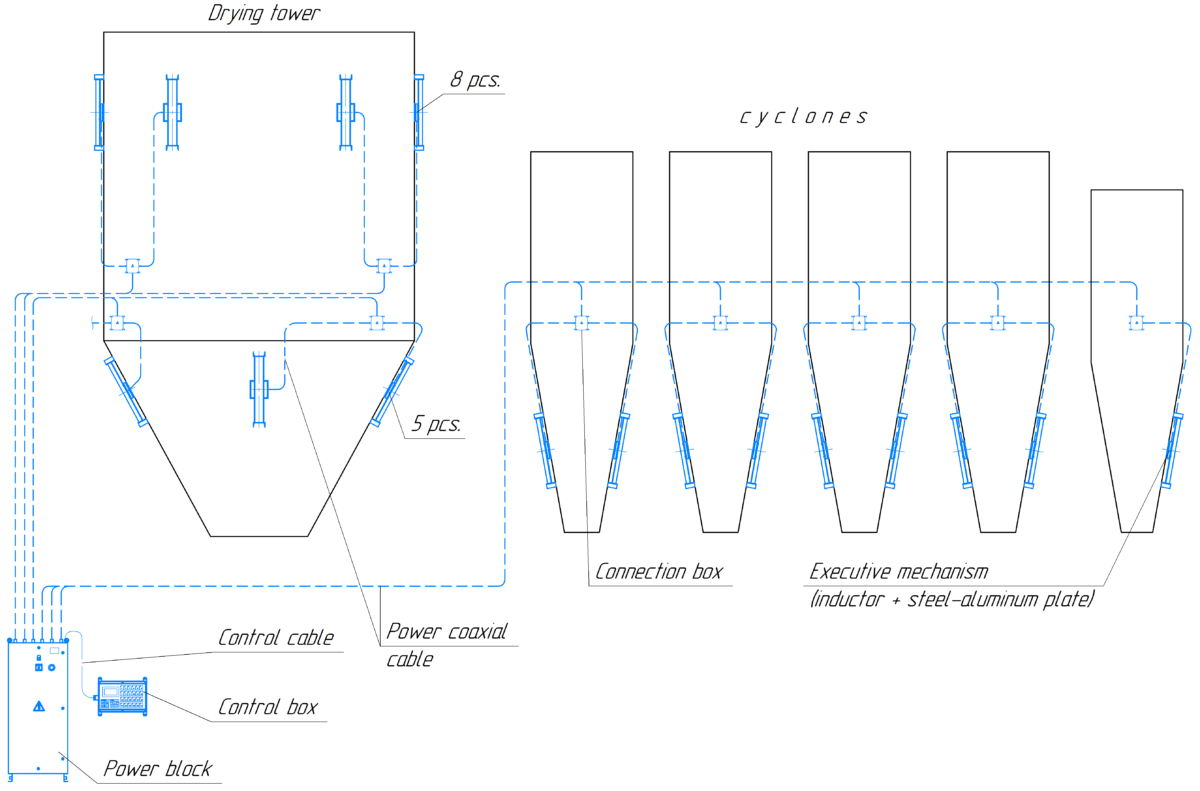
The practice of operating IM installations at various enterprises indicates a higher efficiency of the magnetic-impulse method for cleaning the walls of drying chambers and cyclones in comparison with the traditionally used pneumatic and electromechanical hammers. IM installations are reliable, economical and easy to operate. Electricity consumption by installations of the type IM1-1,2-n, IM2-1,2-n in continuous operating mode – no more than 0.2 kWh. The service life of IM installations before overhauls according to ТУ У3.01-19289902-170-98 is at least 10 years (reference from Kalinovka).
We invite manufacturers of spray drying systems to cooperate with the aim of completing your products with highly efficient IM installations.
Implementations map
Magnetic-impulse installations IM:
- ensure a sustainable release of material from equipped hoppers;
- clean the walls of hoppers from adhered material;
- provide efficient filter regeneration;
- operation in an energy-saving mode, operating costs are minimal;
- basically do not require reconstruction of hoppers when equipping them;
- do not violate the integrity of the walls of the hoppers;
- compatible with strain gauge systems for controlling the weight of material in hoppers;
- comply with the requirements of the Directives and harmonized technical regulation of the European Union on electrical safety and electromagnetic compatibility;
- applicable in hazardous areas of class 22, hazardous by ignition of combustible dust in accordance with the ATEX Directive;
- easily integrated into modern automated process control systems;
- reliable and durable (according to technical conditions – 10 years, in practice, some installations have already been in operation for more than 25 years).