Almost a third of all magnetic-impulse installations IM manufactured by RPE “MITEK” LLC have been introduced at the bakery industry.
Production bins and silos of the bulk storage of flour (BSF) of bakeries and bakeries in the cities of Kiev, Minsk, Krivoy Rog, Nikolaev, Arkhangelsk, Borisov, Zhitomir, Khmelnitsky, Chernigov, Lutsk, Odessa, etc. are equipped with IM installations (see list of implementations).
We suggest you to learn about the video feedback on the practice of the IM installation use:
BSF storage hoppers (from 30 to 120 tons)
Hoppers for bulk storage of flour (BSF) are equipped with IM3-1,1-n installations, where n is the number of installation channels, 2 executive mechanisms in each channel.
Scheme of equipping the BSF hoppers with a magnetic-impulse bridging system based on the IM installation:
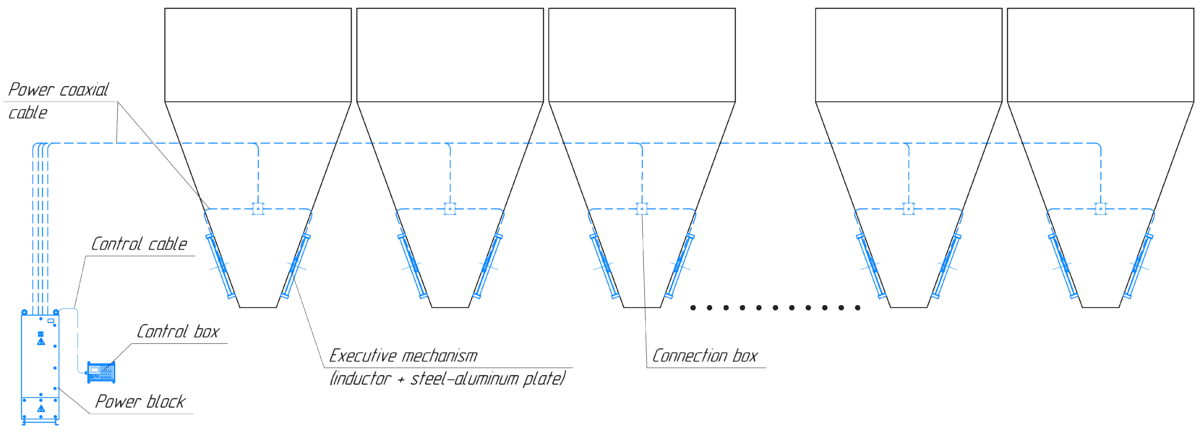
In general, each hopper of the BSF storage is equipped with two executive mechanisms, i.e. the number of installation channels coincides with the number of equipped bins.
BSF hoppers equipped with a magnetic-impulse installation IM:
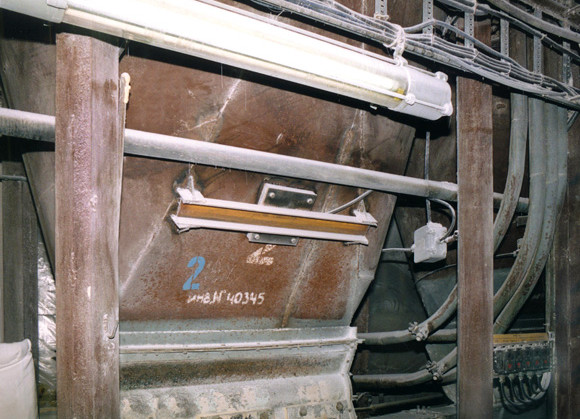
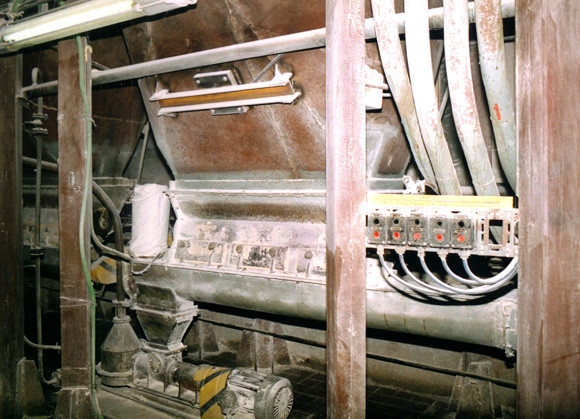
IM installations have also found their application to eliminate suspended flour in storage and production hoppers of confectionery production in the cities of Donetsk, Lugansk, Dnep.
Production hoppers (from 1 to 5 tons)
These hoppers are equipped with installations IM1-1,2-n, IM1-2,4-n, IM3-1,1-n, where n is the number of installation channels, 1 or 2 executive mechanisms in the channel.
Scheme of equipping production hoppers with a magnetic-impulse bridging system based on the IM installation:
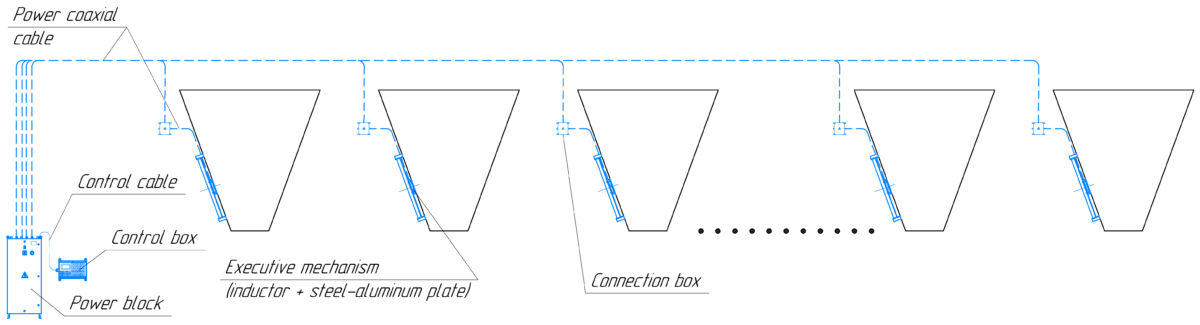
Production hoppers equipped with a magnetic-impulse installation IM:
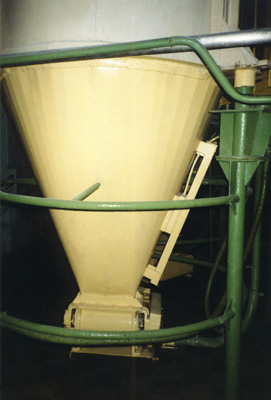
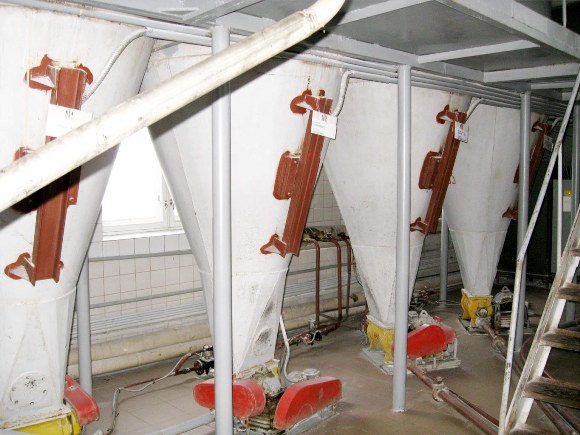
External view of the power block and control box of the IM installation mounted at the bakery:
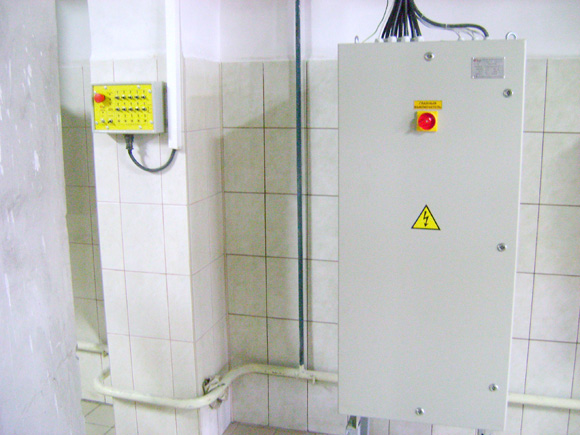
In terms of their efficiency, the installations IM surpass aeration systems and vibration bases, and favorably distinguished from the latter by ease of installation and maintenance, low operating costs and durability of operation.
The service life of the magnetic-impulse installations IM according to TS is not less than 10 years. Long-term practice of operation of IM installations shows that they serve much longer. There is more than 25 years of experience in operating IM installations. At the same time, maintenance costs are practically null, they are limited only by a scheduled inspection of equipment.
With the aim of optimization, it is possible to equip both storage and production facilities with one IM installation, provided their number is small. In this case, a different force effect is envisaged for different objects.
Implementations map
Magnetic-impulse installations IM:
- ensure a sustainable release of material from equipped hoppers;
- clean the walls of hoppers from adhered material;
- provide efficient filter regeneration;
- operation in an energy-saving mode, operating costs are minimal;
- basically do not require reconstruction of hoppers when equipping them;
- do not violate the integrity of the walls of the hoppers;
- compatible with strain gauge systems for controlling the weight of material in hoppers;
- comply with the requirements of the Directives and harmonized technical regulation of the European Union on electrical safety and electromagnetic compatibility;
- applicable in hazardous areas of class 22, hazardous by ignition of combustible dust in accordance with the ATEX Directive;
- easily integrated into modern automated process control systems;
- reliable and durable (according to technical conditions – 10 years, in practice, some installations have already been in operation for more than 25 years).